High Precision Injection Molding: A Catalyst for Business Growth
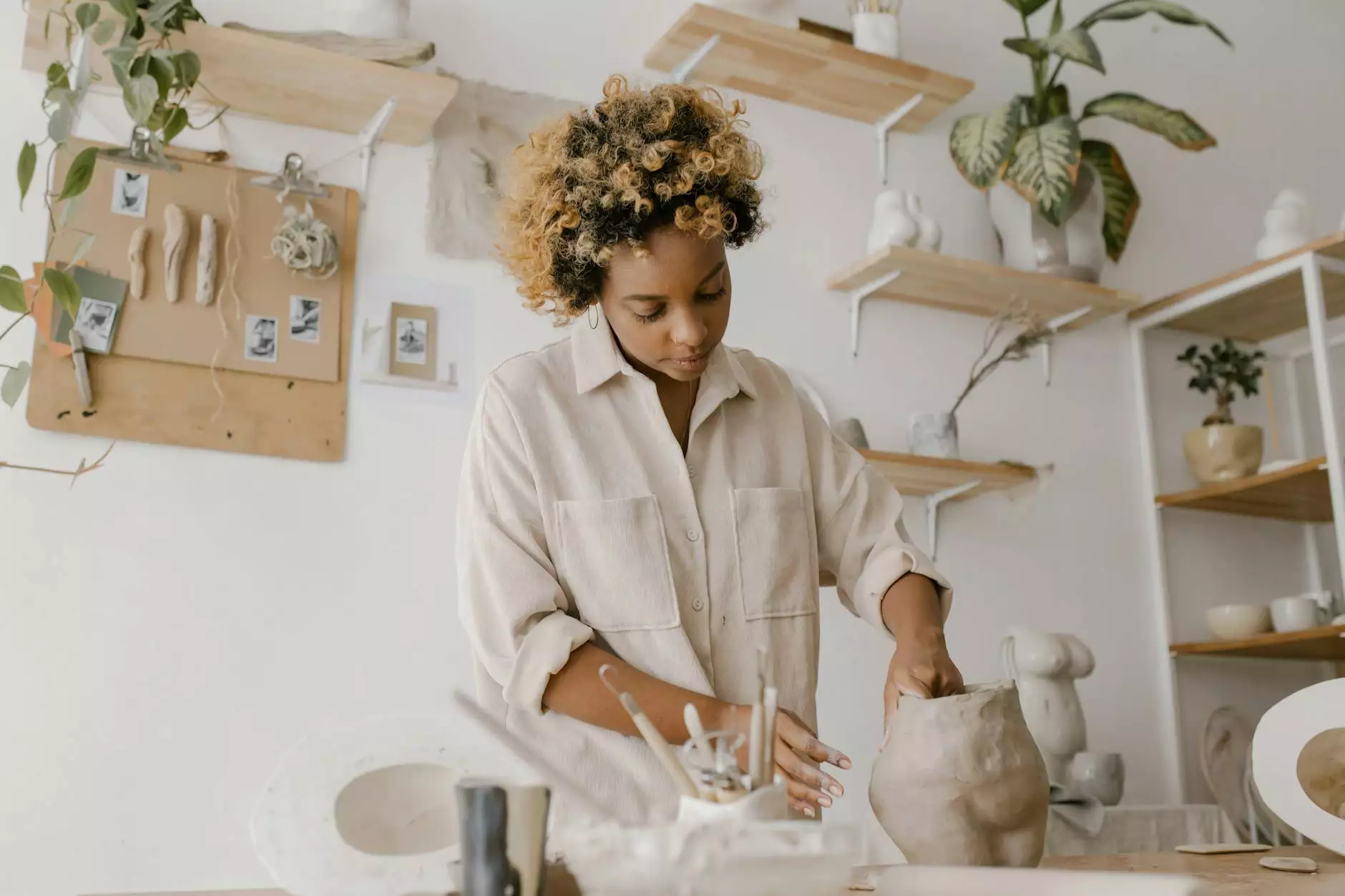
In the world of modern manufacturing, high precision injection molding stands out as a transformative technology that helps businesses streamline their production processes, reduce costs, and enhance product quality. As industries continue to evolve, the need for precision and efficiency becomes paramount. This article delves deep into the realm of high precision injection molding, examining its benefits, applications, and future prospects in a variety of sectors.
What is High Precision Injection Molding?
High precision injection molding is a manufacturing technique that involves the injection of molten plastic into a mold to create intricate parts and components. This process is characterized by its ability to produce high-quality products with tight tolerances and complex geometries. By utilizing advanced machinery and technology, businesses can ensure consistent results and minimize waste, making this method ideal for high-volume production.
The Importance of High Precision Injection Molding in Modern Manufacturing
As industries become more competitive, the demand for high precision injection molding has surged. Here are some of the reasons why this manufacturing technique is essential:
- Cost Efficiency: By minimizing material waste and maximizing production speed, high precision injection molding can significantly reduce manufacturing costs.
- Quality Control: This method allows for stringent quality control measures, resulting in fewer defective products and higher customer satisfaction.
- Scalability: High precision injection molding is perfect for scaling production. Businesses can easily ramp up their manufacturing processes to meet increasing demand.
- Complex Designs: With the ability to create detailed and complex geometries, manufacturers can produce intricate components that traditional manufacturing methods may struggle to achieve.
Applications of High Precision Injection Molding
The applications of high precision injection molding span a multitude of industries, showcasing its versatility:
1. Automotive Industry
In the automotive sector, high precision injection molding is utilized to create various components such as dashboard parts, interior trims, and even small engine components. The reliability of these parts is crucial for safety and performance.
2. Medical Devices
Medical device manufacturing requires the highest standards of precision. High precision injection molding is employed to produce parts like syringes, valves, and housings for diagnostic equipment, where accuracy is crucial for functionality.
3. Consumer Electronics
The consumer electronics industry relies heavily on high precision molding to create components for devices such as smartphones, tablets, and laptops. The compact and intricate designs required for modern electronics demand exceptional precision.
4. Household Goods
From kitchen appliances to personal care products, many everyday items are produced using high precision injection molding. This guarantees not just functional but also aesthetic appeal.
Key Benefits of High Precision Injection Molding
Investing in high precision injection molding offers numerous advantages that can propel a business forward:
- Enhanced Accuracy: Achieving tolerances as tight as ±0.005 mm is standard, making this process ideal for products that require exact specifications.
- Shorter Lead Times: Faster production cycles mean products can reach the market sooner, giving businesses a competitive edge.
- Reduced Material Waste: The design and process efficiency minimize excess waste, aligning with sustainability goals.
- Flexibility in Production: Molds can be adjusted or replaced easily, allowing for quick shifts in production focus depending on market trends.
Challenges in High Precision Injection Molding
While high precision injection molding offers many benefits, challenges also exist:
- High Initial Costs: The investment in advanced machinery and molds can be significant, making it necessary for businesses to weigh long-term benefits against initial expenditures.
- Technical Expertise Required: Operating high-precision injection molding machines and producing complex designs necessitate skilled labor and ongoing training.
- Mold Maintenance: Regular maintenance is essential to ensure molds are kept in optimal condition, which requires time and resources.
The Future of High Precision Injection Molding
Looking forward, the future of high precision injection molding appears bright, driven by technological advancements and growing demand. Some trends to watch include:
1. Industry 4.0 and Smart Manufacturing
The integration of the Internet of Things (IoT) and data analytics into manufacturing processes will revolutionize high precision injection molding. This technology will lead to more efficient operations through real-time monitoring and predictive maintenance.
2. Biodegradable Materials
As sustainability becomes a critical focus, the development of biodegradable materials for injection molding is on the rise. This shift not only addresses environmental concerns but also opens new markets.
3. Additive Manufacturing Integration
Combining additive manufacturing with high precision injection molding may lead to innovative ways to produce molds and components, enhancing design capabilities and reducing lead times.
How to Choose the Right Provider for High Precision Injection Molding
Partnering with the right manufacturer can make a significant difference in the success of your injection molding projects. When looking for a provider, consider the following:
- Experience and Expertise: Choose a provider with extensive experience in high precision injection molding and a solid track record of successful projects.
- Manufacturing Capabilities: Ensure they have modern equipment and technology that can meet your specific needs.
- Quality Assurance Processes: A reputable manufacturer should have stringent quality control measures in place to guarantee product consistency and reliability.
- Customer Service: Strong communication and customer support throughout the project lifecycle can greatly enhance the experience.
Conclusion
In conclusion, high precision injection molding is not merely a fabrication method; it is a vital component that drives innovation and efficiency in manufacturing. As industries advance and consumer demands evolve, the role of high precision injection molding will only grow in importance. Businesses that leverage this technology effectively will not only improve their operational performance but also position themselves at the forefront of their respective markets. By understanding the ins and outs of this process, companies can make informed decisions that lead to long-term success.
For those interested in exploring the transformative potential of high precision injection molding, Deep Mould (deepmould.net) offers exceptional solutions tailored to meet the diverse needs of various industries. From automotive to medical applications, the future of your business could very well depend on the precision and quality achieved through this innovative molding technology.